1. Brief Introduction
The balance block is an important part of the beam pumping unit, its function is to balance the pumping unit The difference in alternating load during the up and down strokes, because the donkey head bears the wheel weight of the liquid column acting on the piston section and the weight of the sucker rod column in the liquid, as well as friction, inertia, vibration and other loads during the up stroke of the pumping unit. Paying a lot of energy: due to the gravity of the sucker rod during the downstroke, the donkey head only bears the downward pulling force. Not only does the motor not need to pay energy, but it does work on the motor. Because the load of the upper and lower strokes is very different, the motor is very It is easy to burn out, causing the pumping unit to not work properly. In order to solve the above problems, a balancing device must be used to reduce the load difference between the upper and lower strokes, so that the equipment can operate normally.
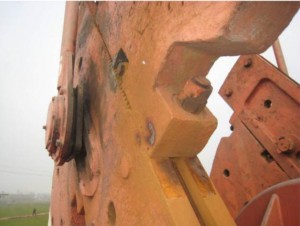
The wheel weight is fixedly connected to the crank with "T" type bolts. With the rotation of the crank, a circular motion is made. A weight of the wheel weight is between 500-1500kg. on the crank. In the beam pumping unit, the crank balance is generally used for heavy machines. The bottom hole load is relatively large, and the influence of various alternating loads makes the balance block easy to loosen. If the balance block loosens and slips, it will cause pumping Accidents such as crooked connecting rods, torn cranks, and pumping units will not only seriously damage wellhead equipment, but even endanger personal safety. Therefore, it is of great significance to analyze the reasons for the loosening of the balance block of the pumping unit and take corresponding measures to reduce the occurrence of accidents and ensure the normal operation of the pumping unit equipment.
2. Cause of bolt looseness
The main reasons for the loosening of the "T" type lug nuts when the oil machine is working are as follows:
(1) Insufficient preload Or, in Courage, in order for the chocolate to go smoothly, but the lug nuts need to be pre-stressed. Difficulties in thread tightening are greatly suppressed. Actively strive to overcome the test of self-reliance on the thread. There is a lot of leverage when it comes to aggressively fighting to stop competition from being put to the test. It is not easy to tighten the bolts, causing the balance weight to loosen easily.
(2) There are defects in the double nut locking method: Double nut locking is a common form of thread anti-loosening in current practical applications. It has the advantages of convenient processing, stability and reliability, and convenient disassembly and assembly. It is widely used in petrochemical, processing and manufacturing industries, but it can only meet general loosening requirements. , The effect is not ideal under repeated alternating loads for a long time, because the fit between the threaded connectors is a clearance fit, and the internal thread and the external thread gradually fit tightly during the pre-tightening process, and the external thread applies an outward Axial force, which in turn generates frictional force opposite to the tightening direction, prevents the bolt from loosening, and thus plays a tightening role. However, due to the gap between the bolt and the nut, the load is constantly changing during the operation of the equipment, so that the pre-tightening force between the inner and outer threads changes, and the threaded connection is slightly loose. This looseness will continue to accumulate over time until the bolt fall off.
(3) Unqualified thread processing quality The processing quality of the threaded parts has a great influence on the connection pair. The common thread gap is uneven. When the thread gap is large, the fitting gap is increased, so that the thread pre-tightening force cannot reach the expectation, and it is difficult to generate enough friction. Accelerates thread loosening under alternating load; when the thread clearance is small, the contact area of the inner and outer threads becomes smaller, and under the action of the load, part of the thread bears the full load, reducing the thread strength and accelerating the failure of the thread connection.
(4) The installation quality does not meet the requirements. When installing, the contact surface should be flat and clean, and the maximum gap should not exceed 0.04 mm. Otherwise, a planer or a file should be used for leveling. If the conditions are not available, a thin iron sheet can be used to level it. If there is oil pollution between the two contact surfaces, the bolts of the balance block will not be tightened tightly, and it will be easy to loosen and slip off.
(5) Influenced by other factors, such as the vibration of the body when the pumping unit stops and brakes, the sudden change of the downhole pressure, etc., it is easy to cause the nut of the balance block to loosen.
3. Precautionary Measures
To prevent the loosening of the threaded connection of the wheel weights, the following corresponding measures should be taken from the three aspects of design, manufacture and installation.
(1) Improve the preload method That is, a scientific method is used to apply a tightening torque that meets its requirements to the tightening bolts to ensure that the threaded connection meets the required pre-tightening force. According to the pre-tightening torque requirements of coupling bolts, the maximum allowable pre-tightening torque of M42-M48 bolts should reach 312-416KGM. According to field experience, it is fine when the wrench bounces slightly.
(2) Add anti-loosening measures In order to ensure the long-term stable operation of the equipment, it is not enough to apply an appropriate pre-tightening force, and certain measures need to be taken to prevent the bolts from loosening. Common anti-loosening measures include the following four:
a. Friction to prevent loosening. This method is similar to the mechanism of increasing the pre-tightening force. By adding accessories, the connecting pair generates a continuous pressure, thereby increasing the frictional force between the thread pairs to prevent them from rotating each other. Common methods include: elastic washers, double nuts, Self-locking nuts, etc. This anti-loosening method is easy to operate and easy to disassemble, but it is easy to loosen under long-term alternating loads.
b. Mechanical anti-loosening. The relative rotation between the threaded pairs is prevented by adding a stopper. Such as the use of split pins, serial wires and stop washers. This method makes disassembly inconvenient, and the stopper pin is easily damaged.
c. Riveting punch to prevent loosening. Welding, hot-melting and other operations are carried out after preloading, which destroys the structure of the thread and makes the thread pair lose the characteristics of the kinematic pair and become an inseparable connection. The disadvantage of this method is that it can only be used once and the bolts must be completely destroyed when disassembling.
d. Structural anti-loosening. Using segmented threads, the positive and reverse threads are combined into one bolt, thus changing the secondary structure of the thread. One bolt can be screwed into either a positive-rotating nut or a reverse-rotating nut. In the opposite direction, locking each other, that is, the way of Down's thread anti-loosening.
Under complex working conditions, due to the long-term influence of alternating moments such as vibration and impact, both the tightening nut and the locking nut tend to loosen, but the tightening nut applies a counterclockwise torque to the locking nut when it is sent back and forth. , and this torque will further tighten the lock nut to the tightening nut, and the two nuts will lock each other so that the threaded connection cannot be loosened. Down's thread does not need to add accessories. It only relies on two nuts with opposite directions to be screwed into the same bolt, and the two nuts are locked with each other. The operation is simple, safe and reliable, but the composite thread structure on the external thread is more complicated. Processing technology requirements are high. In the beam pumping unit, due to the influence of alternating load and vibration, the loosening of the fastening bolts of the wheel weights is very common, and the use of Down's thread to prevent loosening can solve this problem well.
Post time: Sep-16-2022