1. Background Information
Double Mass Fly Wheel (DMFW) is a new configuration that appeared in automobiles in the late 1980s, and has a great effect on the vibration isolation and vibration reduction of automobile power trains.
The lug nuts is to divide the original flywheel into two parts. One part remains on one side of the original engine and acts as the original flywheel to start and transmit the rotational torque of the engine. This part is called the primary mass; the other part is placed on the transmission side of the driveline to improve the rotational inertia of the transmission. , this part is called secondary mass. There is an annular oil cavity between the two parts, and a spring shock absorber is installed in the cavity, which is responsible for connecting the two parts of the flywheel, as shown in Figure 1. The secondary mass can increase the inertia moment of the drive train without increasing the inertia moment of the flywheel, and reduce the resonance speed below the idle speed.
The Hexi base engine factory produces 5 dual-mass flywheel engines, namely EK/CM/RY/SN/TB. The dual-mass flywheels of these 5 engines are tightened by an automatic station (OP2135), and the bolts for tightening the dual-mass flywheels are Torx bolts. The tightening accuracy is required to be high, and a slight deviation in the angle will cause the tightening to be incorrect to the shaft. On average, 15 unqualified products appeared in each shift, resulting in a large number of repairs and affecting the normal operation of the production line.
At present, the double-mass flywheel tightening station adopts the control method of torque plus angle (35±2)N m+(30~45)° to monitor the bolt torque. In addition, the static torque of the dual-mass flywheel bolt is large (technical requirements: 65 N·m ~ 86 N·m). In order to meet the torque requirements, it is required that the sleeve (as shown in Figure 3) and the bolt should be aligned more accurately during the tightening process. For this reason, this paper conducts investigation and analysis based on actual problem cases, and proposes relevant solutions on how to improve the qualified rate of double-mass flywheel bolt tightening.
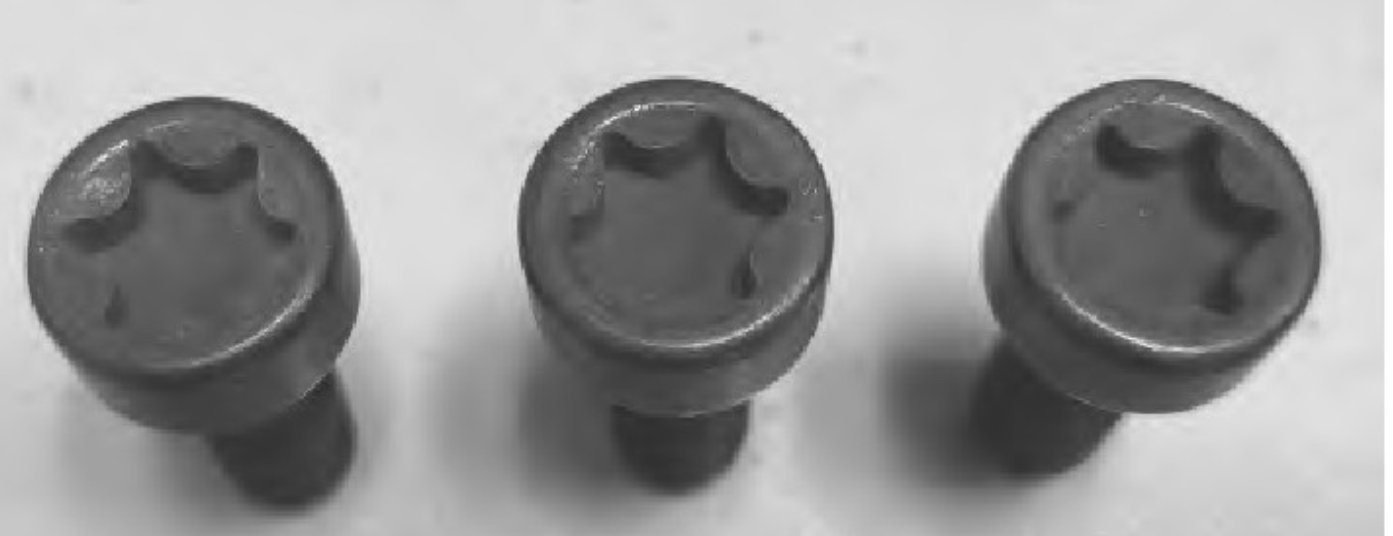
2. Investigation of Unqualified Tightening of Lug Nuts
The problem of "tightening incorrectly to the Lug Nuts" accounted for 94.63% of the total number of unqualifieds, which was the main problem causing the low qualified rate of double-mass flywheel bolt tightening. After determining the crux of the main problem, we can prescribe the right medicine. Combined with the scene and production situation, the main research direction has been clarified.
According to the data of the status quo investigation, the data of 459 dual-mass flywheel bolts from January to March 2021 were not tightened and the shaft data were analyzed, as shown in Table 1 and Figure 6. After analysis, it was found that 25 of the dual-mass flywheel bolts failed to be tightened due to Unpredictable factors such as misjudgment by the camera of the equipment, improper operation of the pallet, loss of the origin of the equipment, damage to the sleeve, etc., have greater randomness. Therefore, the main crux of this problem can be solved theoretically to a degree of 1-25/459=94.83%.
3. Solution
1. The solution to the wear of the tooling teeth of the flywheel jaws
Checking the on-site flywheel claw tooling, it was found that the teeth of the flywheel claw tooling were severely worn, and the teeth could not effectively engage the flywheel ring gear. During the tightening process of the equipment, the flywheel shakes, causing the sleeve to be misaligned with the bolt. During the tightening process, the sleeve jumps out of the bolt, or idly rotates on the surface of the bolt, resulting in unqualified tightening.
Replace the new flywheel claw tooling, the date of use is marked on the flywheel claw tooling, and the tooling should be replaced every 3 months to avoid the flywheel shaking during the tightening process due to the wear of the claw, which will cause the unqualified shaft to occur.
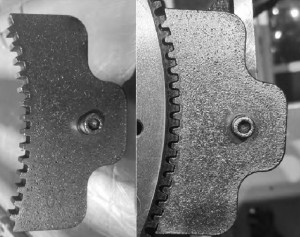
2. The solution for the loosening of the tray bayonet
Check the on-site pallet rework records. The reworked engine pallets are often concentrated in 021#/038#/068#/201#. Then the pallets were inspected and found that the pallet fixing pins were loose. As a result, the sleeve is not aligned with the bolt, the sleeve jumps out of the bolt during the tightening process, or idling on the surface of the bolt results in unqualified tightening. If the fixing bolts of the pallet bayonet are loosened, the bayonet cannot be effectively fixed. For the fixing block of the pallet, use extended bolts (previously short bolts), and use anti-reverse loosening nuts to fix them to avoid the bayonet bayonet caused by the loosening of the pallet bayonet fixing bolts. It cannot be effectively fixed, resulting in the flywheel shaking and misaligning the shaft during the tightening process, which is not qualified.
3. Optimize the method of taking pictures of the device camera
This step is the most difficult part of the plan. Because there are no parameters to refer to, it is necessary to explore and control the equipment. Specific plan:
(1) Re-correct the origin coordinates
(2) Increase the camera's photo center compensation parameter program, such as the center hole offset of the photo, set the compensation value and correction amount for the center coordinates, and correct the center hole offset position
(3) Adjust Camera exposure compensation value.
The data was continuously tracked and collected for 3 months. During this period, the qualified rate of double-mass flywheel bolt tightening fluctuated, and appropriate corrections and adjustments were made to the photographing parameters. At the beginning of April, the exposure compensation value was adjusted from 2 800 to 2 000, and the tightening qualification rate increased to 97.75%. , there were more failures after the tracking operation, and then the camera exposure value was adjusted: from 2 000 to 1 800, which increased to 98.12%; in order to consolidate the measures, during the tracking process, the camera exposure value was optimized again: from 1 800 became 1 000, and the final tightening pass rate in April increased to 99.12%; the tightening pass rate in May and June was continuously tracked to over 99%.
4. Eeding
The lug nuts flywheel is the device with the best vibration isolation and vibration reduction effect on the current automobile. The vibration of a diesel engine is larger than that of a gasoline engine. In order to reduce the vibration of the diesel engine and improve the riding comfort, many diesel passenger cars in Europe now use dual-mass flywheels, so that the comfort of a diesel engine car is comparable to that of a gasoline engine car [6]. In China, FAW-Volkswagen's Bora manual transmission sedan took the lead in adopting dual-mass flywheels. The market demand for dual-mass flywheels continues to expand, and the requirements for tightening qualification rates are also getting higher and higher [7]. This article analyzes the common problems that lead to unqualified double-mass flywheel tightening, finds the root cause, formulates problem solving methods, and fundamentally solves the problem. At present, the equipment is running well, and the pass rate remains above 99%. The solution of this problem has positive significance for saving labor costs and improving quality of the factory.
Post time: Sep-29-2022