By comparison, the most optimal scheme of the integrated reactor main nut vertical cleaning machine is proposed. The main bolts and bolts can be checked and oiled only once and again. Principle Principle The principle principle uses the spreader to hoist the bolt vertically into the loading and unloading function. The nut is followed by the active principle. Detect and detect and generate a thread development diagram, the product has less radioactive waste and occupies a small area. This equipment has been successfully applied in the nuclear power field, and can fully meet the needs of the main bolts of the reactor pressure vessel.
Some representative existing RPV main bolt and nut cleaning machines are as follows:
(1) The first-generation washing machine of CNNC Wuhan Nuclear Power Operation Technology Co., Ltd. (hereinafter referred to as CNPO) adopts a horizontal type.
(2) The Institute of Optoelectronic Technology, Chinese Academy of Sciences adopts horizontal cleaning , and the equipment is integrated.
(3) China Nuclear Power Research and Design Institute adopts vertical cleaning.
1. Research Question
After the nuclear power plant reactor pressure vessel has been in operation for a period of time, the oil stains and other impurities on the main bolts and nuts have been solidified in a high-temperature and high-pressure environment. If they are not cleaned in time, on the one hand, it may cause thread seizure, and on the other hand, it will affect subsequent in-service inspections. implementation, resulting in signal anomalies and misjudgments. The cleaning of RPV main bolts and nuts is one of the tasks to ensure that the RPV main bolts are in a safe and reliable state for a long time. Therefore, it is necessary to efficiently clean the RPV main bolts and nuts.
In order to improve the efficiency of the cleaning machine and meet the needs of the power plant with less floor space, less waste liquid and high safety, after a comprehensive comparison, it is concluded that the vertical cleaning machine with a highly integrated system is the best solution.
In view of this, we independently developed the RPV main bolt and nut vertical cleaning machine with a higher degree of automation, which can complete automatic nut loading and unloading, bolt and nut cleaning and air drying, as well as thread machine visual inspection and bolt oiling in one hoisting.
2. The Main Problems
In this study, on the basis of inheriting the common technology and knowledge achievements of horizontal cleaning machines and ensuring the cleaning effect, the cleaning process is optimized, and a RPV main bolt and nut vertical cleaning machine with a higher degree of automation is designed and developed, specifically including the following aspects:
(1) The design of the hoisting method of the bolt assembly.
(2) The design of the realization method of automatic loading and unloading of nuts.
(3) The realization method design of simultaneous vertical cleaning of bolts and nuts.
(4) The design of the realization method of thread machine vision inspection.
(5) Control system implementation design.
3. Research Process and Method
The main bolt and nut vertical cleaning machine has the functions of automatic nut loading and unloading, thread cleaning, air drying, machine visual inspection of bolt threads, and oiling.
The washing machine system is highly integrated, and the main layout is as follows: The bolt and nut cleaning unit is located in the middle of the washing machine, and the gear pump for extracting waste liquid is arranged at the lower part, and the liquid storage tank and filter of the cleaning liquid circulation system are respectively installed in the left box. , magnetic pump, waste liquid tank and fan and filter of pneumatic air supply and exhaust system. An image acquisition component is installed outside the bolt cleaning box for thread machine vision inspection. A cantilever structure is installed on the top of the cabinet, and the display screen installed at the end of the cantilever is used for equipment operation. Bolts wash the rear of the box for the installation of control components. A sealed door is installed in front of the bolt cleaning box, and glass is installed on the door to facilitate observation of the cleaning status. The sealed door is pressed at 3 points to ensure the sealing effect (see the figure below).
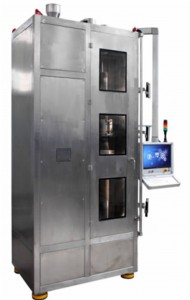
The main advantages of this cleaning machine are:
(1) All functions can be completed in one hoisting.
(2) The nut can be loaded and unloaded automatically.
(3) Clean the nuts and vertical bolts at the same time.
(4) It has the function of thread machine vision inspection and generates thread development diagram.
The implementation process of these main advantages and functions will be introduced in detail below.
3.1 Lifting of Bolt Assembly
The bolt and nut assembly is hoisted from the bolt storage basket to the main bolt tray inside the bolt and nut cleaning machine through a special C-shaped spreader (see Figure 2).
3.2 Automatic loading and unloading of nuts
(1) Equipment composition
The nut automatic loading and unloading unit is integrated inside the cleaning box. It mainly includes bolt driving mechanism, nut lifting mechanism and bolt clamping mechanism.
The bolt driving mechanism is mainly composed of the main bolt tray and the bolt driving geared motor.
The nut lifting mechanism is mainly composed of a main nut fixing clip, a driving slider, a follower slider, a trapezoidal screw, a guide optical axis and a screw driving motor.
The stud clamping mechanism is used to fix the main screw clamp in the box. It is a two-half circular arc clamping structure and is installed on the inner frame of the cleaning box.
(2) Functional reality
Nut loading and unloading bolts, nuts, nuts, active mechanism, can be mechanism, can ensure that the thread is not free from damage. . At the same time, users simultaneously
The nut removal procedure is as follows:
The main bolt rotates counterclockwise, the needle rotates, the nut rotates, the needle rotates, and then rotates in the circumferential direction, only rotates, and can only move in the direction of rotation, while moving along the axis, the movement guide rises and the bar drives the rotation, Make the motor motor motor motor motor slider slider slider one same same same same rise rise rise rise rise rise rise, two passive sliders slider rotate rotate rotate rotate rotate rotate rotate rotate rotate rotate two sliders slider rotate rotate Rotate and rotate to prevent the impact on the first threading of the nut when tripping.
The nut breaks away from the threaded section, the main bolt, the main bolt rotates, the active rotation, and the movement, and, with the follow-up, with the slide block, pushes the contact, pushes, pushes the follow-up follow-up follow-up slide block slide block. So far the automatic disassembly operation of the main nut is completed.
Installed the program and vice versa.
Cleaning is mainly divided into internal thread cleaning of the main nut and three-stage external thread cleaning of the main bolt. Since the main nut is located directly above the main bolt, in order to prevent the cleaning liquid flowing down the main nut from polluting the cleaned bolts, after the cleaning of the bolts and nuts is completed, Bolts add a rinse step.
(1) Nut cleaning
Nut cleaning is mainly completed through the cooperation of the nut cleaning brush and the nut lifting mechanism. The nut cleaning brush and the driving motor are installed on the upper top cover of the cleaning machine.
The nut cleaning brush is mainly composed of a cleaning brush head, a main shaft and a support cylinder. The cleaning brush head is a centrifugal structure. When it is not rotating, the outer envelope diameter of the cleaning brush is smaller than the inner diameter of the nut. When the brush head rotates, the brush fixing seat is opened under the action of centrifugal force, and the nylon brush installed on the fixing seat is close to the nut. Nut internal thread surface.
Before the nut is cleaned, the nut lifting mechanism is used to raise the nut and be inserted into the cleaning brush head, and then the nut cleaning brush drive motor is started to rotate the cleaning brush head. While the brush head is rotating, the main nut moves up and down under the drive of the lifting mechanism, so as to clean the entire thread section.
(2) Bolt cleaning
The bolt cleaning unit is mainly composed of a roller brush assembly, a roller brush swing mechanism, a main bolt fixing device and a main bolt driving device. The roller brush assembly is connected with the piston rod of its swing cylinder through the roller brush swing rod. When the piston rod of the rolling brush cylinder is pushed out, the rolling brush assembly swings close to the threaded section of the main bolt, and when retracted, the rolling brush assembly is away from the main bolt. The roller brush driving motor drives the roller brush to rotate through the belt pulley.
When cleaning the main bolts, the main bolt drive motor drives the main bolts on the tray to rotate, the swing cylinder moves the roller brush assembly closer to the three-segment thread of the main bolt, starts the roller brush drive motor, and the roller brush rotates against the surface of the main bolt. The main bolts can then be cleaned.
During the cleaning process, the cleaning liquid circulation system supplies the cleaning liquid to the liquid spray pipe, and multiple nozzles are installed on the liquid spray pipe to evenly spray the cleaning liquid onto the bolt surface.
4. Problems and Solutions
In the research and design process, in order to verify the performance of the equipment, a large number of tests were carried out with the bolt and nut simulation body after the equipment was manufactured, and some problems were found during the process, and corresponding solutions were taken.
(1) Leakage of the cleaning box
Since the equipment is a vertical structure, this puts forward higher requirements on the sealing of the box. During the cleaning process, it was found that part of the cleaning liquid splashed to the inner side of the airtight door and the frame, and then flowed down, causing leakage. Take the following steps in this regard:
(2) During the whole cleaning and air-drying process, the fan is always in the suction state to ensure that the air pressure in the cleaning box is lower than the atmospheric pressure and is in a negative pressure state, which effectively prevents the overflow of waste liquid and waste gas in the box, and fully guarantees the safety of operators.
(3) The surface of the stainless steel parts inside the sealed door of the cleaning box is sprayed with a super-hydrophobic coating, and the door glass is also treated with hydrophobic treatment, so that the water droplets splashed on the sealed door during the cleaning process will not adhere to the door panel and glass, thereby improving the residual water droplets on the door panel falling problem.
(2) Bolt slipping phenomenon
Initially, the main bolt tray adopts the structural form of bonding rubber plates on the metal parts. When the driving torque is too large, the rubber and the bottom of the bolts will slip and play a protective role.
In the early stage of commissioning, water was used as the cleaning medium, and the driving effect of the main bolt was good; in the later stage, after the cleaning medium was replaced with the cleaning fluid actually used in nuclear power plants, it was found that the main bolt could not be driven and slipped. After analysis, the original bolt driving method was invalid due to the lubricating effect of the cleaning fluid.
By canceling the structure of bonding the rubber plate on the metal parts on the main bolt tray, 4 spherical plungers are directly installed on the main bolt tray. When the main bolt is driven, the 2 spherical plungers slide into the groove at the bottom of the main bolt , to realize the driving of the main bolt, if the driving torque is too large, the protection can also be realized. At the same time, the main bolt driving servo motor is also equipped with torque protection. When the main bolt driving torque exceeds the set value, it will stop and alarm.
(4) Air drying effect is not good
After debugging, we found that the bolts were not fully air-dried, and the effect needs to be improved.
By studying the air-drying process of the equipment, it was found that in the early stage of commissioning, the bolt roller brush only moves closer and rotates at high speed when the bolt is cleaned to remove surface stains. After the air-drying process starts, the bolt roller brush leaves the bolt, and the bolt is air-dried only by the high-speed jet of compressed air.
For this reason, the author improves the air-drying process. After cleaning, when the air-drying flow starts, the roller brush moves close to the bolt and then rotates at a high speed to remove surface liquid. After 1/3 of the air-drying cycle, the bolt roller brush leaves the bolt and stops rotating, and then continues Bolts are dried by a high-speed jet of compressed air.
Practice has proved that after the improvement, the air-drying effect is greatly improved.
Post time: Nov-17-2022