History:
The balancer has a history of more than 100 years. In 1866, the German Siemens invented the generator. Four years later, a Canadian, Henry Martinson, patented the balancing technique, launching the industry. In 1907, Dr. Franz Lawaczek provided Mr. Carl Schenck with improved balancing techniques, and in 1915 he produced the first double-sided balancing machine. Until the late 1940s, all balancing operations were performed on purely mechanical balancing equipment. The balance speed of the rotor usually takes the resonant speed of the vibration system to maximize the amplitude. It is not safe to measure rotor balance in this way. With the development of electronic technology and the popularization of rigid rotor balance theory, most balance devices have adopted electronic measurement technology since 1950s. Tire balancer of the planar separation circuit technology effectively eliminates the interaction between the left and right sides of the balancing workpiece.
The electric measuring system has gone through the stages of Flash, watt-meter, digital and microcomputer from scratch, and finally appeared the automatic balancing machine. With the continuous development of production, more and more parts need to be balanced, the larger the batch size. In order to improve labor productivity and working conditions, the balancing automation was studied in many industrial countries as early as the 1950s, and semi-automatic balancing machines and dynamic balancing automatic lines were produced successively. Because of the need of production development, our country began to study it step by step in the late 1950s. It is the first step in the research of dynamic balancing automation in our country. In the late 1960s, we began to develop our first CNC six cylinder crankshaft dynamic balance automatic line, and in 1970 successfully trial-produced. The microprocessor control technology of the balance testing machine is one of the development directions of the world dynamic balance technology.
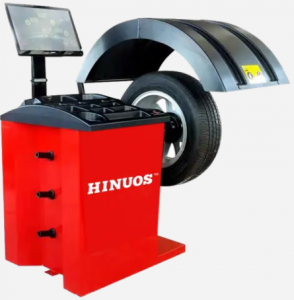
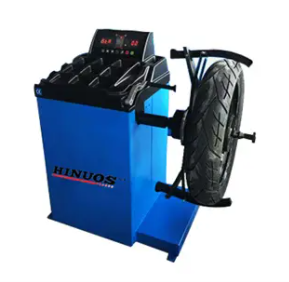
Gravity type:
The gravity balancer is generally called the static balancer. It relies on the gravity of the rotor itself to measure static unbalance. It is placed on the two horizontal guide rotor, if there is an imbalance, it makes the axis of the rotor in the guide rolling moment, until the imbalance in the lowest position only static. The balanced rotor is placed on a support supported by a hydrostatic bearing, and a piece of mirror is embedded under the support. When there is no imbalance in the rotor, the beam from the light source is reflected by this mirror and projected to the polar origin of the imbalance indicator. If there is imbalance in the rotor, the rotor pedestal will tilt under the action of the gravity moment of the imbalance, and the reflector under the pedestal will also tilt and deflect the reflected light beam, the spot of light that the beam casts on the polar coordinate indicator leaves the origin.
Based on the coordinate position of the deflection of the light point, the size and position of the imbalance can be obtained. In general, rotor balance includes two steps of unbalance measurement and correction. The balancing machine is mainly used for unbalance measurement, and the unbalance correction is often aided by other auxiliary equipment such as drilling machine, milling machine and spot welding machine, or by hand. Some balancing machines have made the calibrator a part of the balancing machine. The signal detected by the small sensor of the support stiffness of the balancer is proportional to the vibration displacement of the support. A hard-bearing balancer is one whose balancing speed is lower than the natural frequency of a rotor-bearing system. This balancer has a large stiffness, and the signal detected by the sensor is proportional to the vibration force of the support.
Performance indicators:
The main performance of the tire balancer is expressed by two comprehensive indexes: the minimum remaining unbalance and the unbalance reduction rate: the Balance Precision Unit G.CM, the smaller the value is, the higher the precision is; The period of unbalance measurement is also one of the performance indexes, which directly affects the production efficiency. The shorter the balance period is, the better.
Post time: Apr-11-2023