The Production Process of Wheel Weights
Wheel weights play a crucial role in the automotive industry, ensuring that vehicles maintain proper balance and stability. These small yet significant components are essential for the smooth operation of wheels, particularly in vehicles that require precise alignment and weight distribution. In this article, we will delve into the production process of wheel weights, exploring the materials used, manufacturing techniques, and quality control measures that ensure their effectiveness.
Understanding Wheel Weights
Before we dive into the production process, it’s important to understand what wheel weights are and why they are necessary. Wheel weights are small metal or plastic pieces attached to the rim of a wheel to balance it. When a wheel is not properly balanced, it can lead to uneven tire wear, vibrations, and decreased fuel efficiency. By adding wheel weights, mechanics can ensure that the weight is evenly distributed around the wheel, enhancing the vehicle's performance and safety.
Materials Used in Wheel Weight Production
The production of wheel weights involves various materials, each chosen for its specific properties. The most common materials include:
1. Lead: Traditionally, lead has been the material of choice for wheel weights due to its density and malleability. However, due to environmental concerns and regulations, the use of lead has been declining.
2. Zinc: Zinc is becoming increasingly popular as a substitute for lead. It is less toxic and offers similar weight properties, making it an excellent alternative for wheel weights.
3. Steel: Steel wheel weights are also common, particularly for larger vehicles. They are durable and can withstand harsh conditions, although they may be heavier than their zinc or lead counterparts.
4. Plastic: Some wheel weights are made from plastic, particularly for lighter vehicles. These weights are often used in conjunction with adhesive backing for easy application.
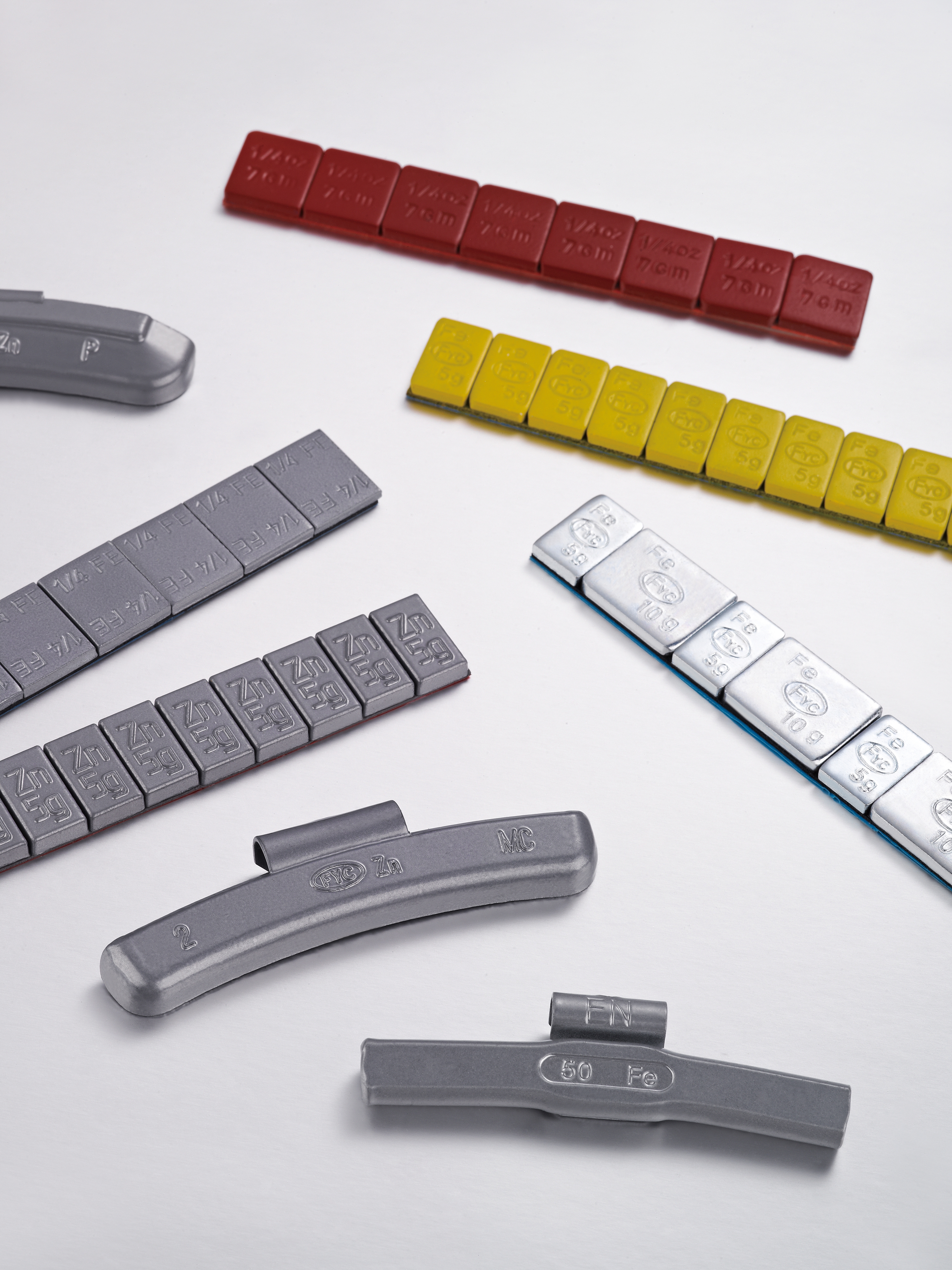
The Production Process of Wheel Weights
The production of wheel weights involves several key steps, from material selection to final quality checks. Here’s a detailed look at each stage of the process:
Environmental Considerations
1. Material Selection
The first step in the production process is selecting the appropriate material. Manufacturers must consider factors such as weight, cost, environmental impact, and regulatory compliance. Once the material is chosen, it is sourced from suppliers and prepared for manufacturing.
2. Melting and Casting
For metal wheel weights, the next step is melting the selected material. This process typically occurs in a furnace where the metal is heated to its melting point. Once melted, the liquid metal is poured into molds to create the desired shape and size of the wheel weights.
- Lead Casting: In the case of lead, the molten metal is poured into molds that are designed to create specific weight configurations. After cooling, the weights are removed from the molds.
- Zinc and Steel Casting: Similar processes are used for zinc and steel, although the melting points and techniques may vary slightly due to the different properties of these metals.
3. Machining and Finishing
After casting, the wheel weights often require additional machining to achieve precise dimensions. This may involve cutting, grinding, or drilling to ensure that the weights fit perfectly on the wheel rims.
Finishing processes, such as coating or painting, may also be applied to enhance the appearance and protect the weights from corrosion. For example, zinc weights may be coated with a layer of zinc to prevent rusting, while plastic weights may be colored for aesthetic purposes.
4. Quality Control
Quality control is a critical aspect of the production process. Manufacturers implement rigorous testing procedures to ensure that each wheel weight meets industry standards and specifications. This may include:
- Weight Testing: Each weight is weighed to ensure it meets the specified tolerance levels.
- Dimensional Inspection: Measurements are taken to confirm that the weights are within the required dimensions.
- Durability Testing: Weights may be subjected to stress tests to evaluate their performance under various conditions.
5. Packaging and Distribution
Once the wheel weights have passed quality control, they are packaged for distribution. Packaging is designed to protect the weights during transportation and storage. Manufacturers often provide detailed labeling, including weight specifications and installation instructions, to assist mechanics and consumers.
The final step involves shipping the packaged wheel weights to retailers, automotive shops, and manufacturers, where they will be used in vehicle assembly or maintenance.
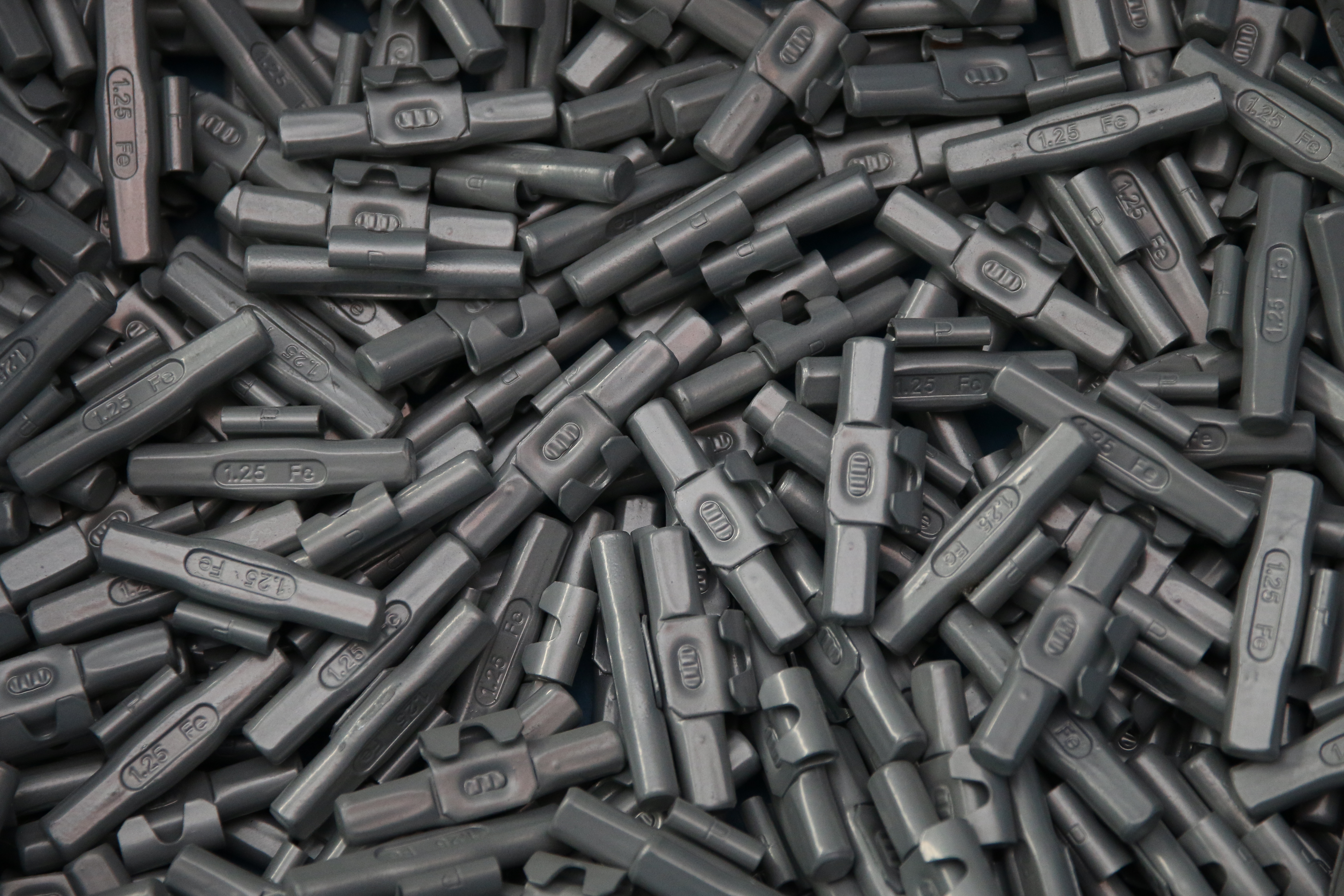
As the automotive industry becomes increasingly aware of environmental issues, the production of wheel weights has also evolved. The decline in lead usage is a direct response to environmental regulations aimed at reducing toxic materials. Manufacturers are now focusing on sustainable practices, such as recycling materials and minimizing waste during production.
Additionally, the shift towards lighter materials, such as plastic and zinc, reflects a broader trend in the automotive industry to improve fuel efficiency and reduce emissions. By using lighter wheel weights, vehicles can achieve better performance while also being more environmentally friendly.
Conclusion
The production process of wheel weights is a complex and meticulous endeavor that plays a vital role in the automotive industry. From material selection to quality control, each step is designed to ensure that these small components effectively contribute to vehicle performance and safety. As the industry continues to evolve, manufacturers are adapting their processes to meet environmental standards and consumer demands, paving the way for a more sustainable future in automotive manufacturing.
Understanding the intricacies of wheel weight production not only highlights the importance of these components but also underscores the ongoing innovations within the automotive sector. As technology advances, we can expect further improvements in the materials and methods used to produce wheel weights, ultimately enhancing the driving experience for consumers worldwide.
Post time: Oct-10-2024